Part Design: A Guide to Designing Plastic Living Hinges for Injection Molding
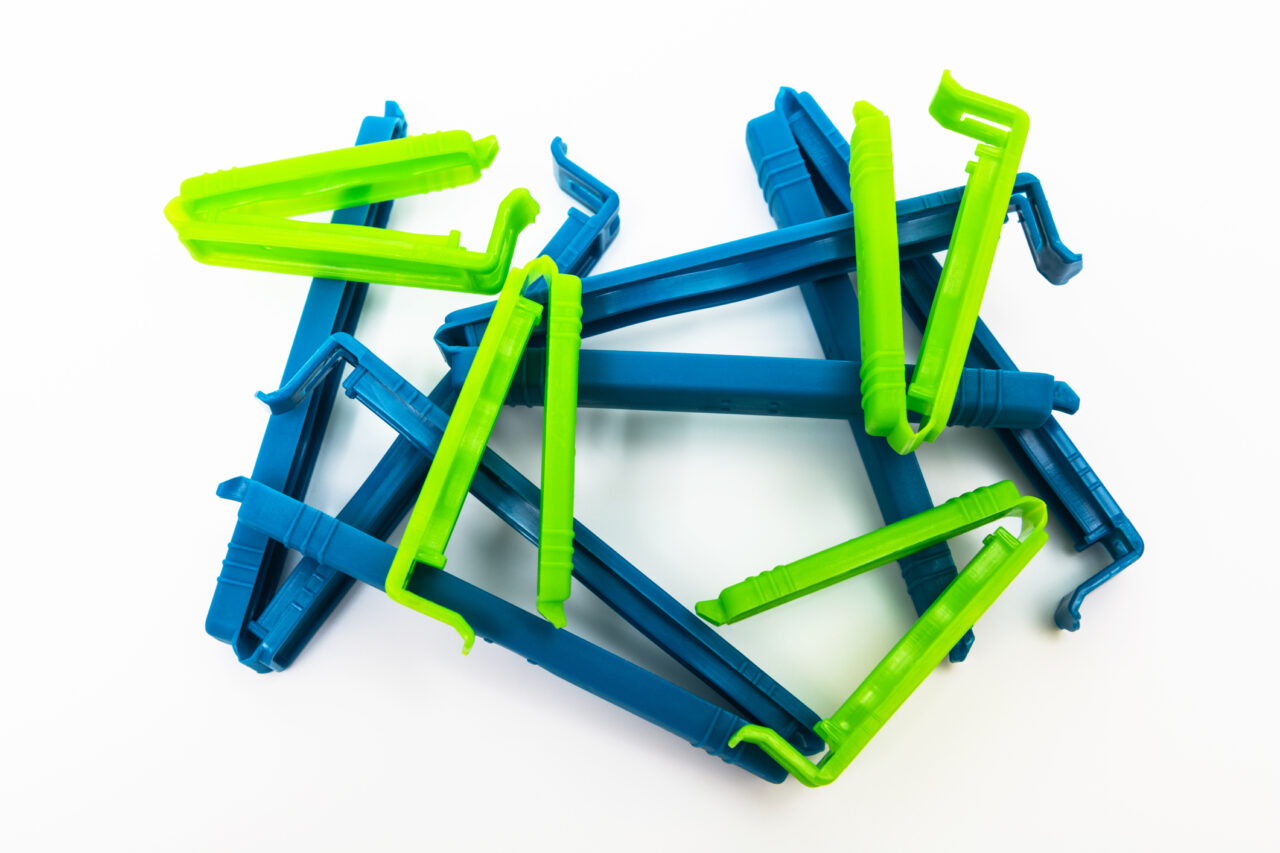
Introduction to Plastic Living Hinges:
A plastic living hinge is a part design feature that uses a thin plastic material to join two larger plastic bodies of the same material. In other words, a living hinge is an extension of the common material between the two plastic parts. These types of hinges are common features in product design for several reasons. For instance, they are easy to manufacture, reduce production costs, and improve the end-user experience. Take this for example:
Remember when you had to unscrew the cap on the ketchup bottle before you doused your hot dog in tomato goodness?
With plastic hinges, the condiment bottle manufacturers removed a simple inconvenience. They replaced the screw top with the easy-to-use, pop-off white caps we know today. A feat in mechanical engineering if you ask me. Yet, this was not the only way living hinges revolutionized plastic products. There are more examples that span over many different industry segments. We’ll get to those shortly.
In this article, you’ll learn what a living hinge is and how it is produced in a manufacturing environment. Also, we’ll highlight the features and benefits of using them in your part design. Our process involves using thermoplastic materials, the main ones being polypropylene and polyethylene. By the end of the article, you should have everything you need to design a living hinge for your next project.
What is a Living Hinge?
The definition of a living hinge is a thin section of plastic that connects two large plastic pieces. In our ketchup cap example, this would be the base of the cap and the lid. The two of which are joined by a thin and flexible plastic- the hinge. In this case, the cap uses what is called a butterfly hinge. There are four types of living hinges that we’ll talk about later in the post.
What are living hinges used for?
Living hinges allow for the two aforementioned plastics pieces to rotate along a thin hinge line. This gives the part greater rotational mobility – usually 180 degrees or more. This mobility is one of the prime reasons why designers love to use living hinges. For instance, some applications are designed around rotational mobility being the core feature because it makes the product easier to use. Ultimately, this improves the overall product’s look, usability, and function.
Aside from improved usability, a living hinge also requires fewer manufactured components. For example, a container that uses two-piece hinges requires multiple parts for the hinge to work. Unlike the traditional hinge, the living hinge is an extension of the container itself. The result – a living hinge has fewer parts to assemble and simpler tooling requirements. These two factors eat up a large chunk of the manufacturing costs. Overall, using a living hinge design has three key features:
To summarize, the main reasons that living hinges are used for are:
- Improving a design
- Reducing manufacturing costs
- Giving the user a better experience with the product
Why should I consider a living hinge for my part?
If you’re thinking about using a living hinge versus a traditional hinge there are a few things you need to consider. One thing is how much the design affects your manufacturing costs and process. If your product is compatible with a living hinge design, then you might be able to save some money. However, the opposite is true that a poorly designed hinge will lead to more manufacturing costs down the line.
Another consideration for living hinges is how it will affect your customers. A well-designed living hinge can change the way customers view and use your product. However if the design doesn’t make the product easier to use, more affordable, or look better, then it is best left alone. Ultimately, you should consider a living hinge if you believe it will improve how customers view and use your product.
Now, let’s talk about the benefits of a living hinge design versus other hinges.
The Benefits of a Living Hinge Design vs Traditional Hinges
There are three main benefits from using a living hinge design:
- Less manufacturing costs – In most cases, a living hinge is less costly than its traditional counterparts. In the context of injection molding, a traditional hinge would require cutting another cavity into the mold plate. In other words, you would have to make accommodations for an additional component for both manufacturing and assembly. On the other hand, you might even cut a check for an entirely separate tool to produce just the hinge(s). This will quickly add to your piece part price even if the tool build is simple. With the living hinge, the entire “assembly” can be made using one to two cavities, so no extra costs. Your tooling cost would be less expensive because you would also eliminate an assembly step.
- Better user experience– How a customer experiences your product is every bit as important as how it’s made. We’ve discussed the consequences of a poor design, but what about a good design? There are many opportunities where a well-designed living hinge can change the way customers view a product. The ketchup bottle cap was an obvious one because it changed the way manufacturers made condiment bottles. Now, Heinz was already a market leader in this category. But a design like that could help a lesser-known company become a fan favorite!
- Durability and flexibility– We’ve talked about the ketchup bottle cap many times now- Are you worn out from it? Well, the cap is still going strong, bending at the hinge with exceptional rotational mobility. And that’s exactly what it’s made for! A living hinge has an incredible lifespan even after it’s activated millions of times.
Now that we’ve gone over some of the main reasons why designers use living hinges, we’ll start talking about the characteristics that make these designs so adaptable.
What Are the Characteristics of a Living Hinge?
Performance characteristics
- Application – Living hinges by nature are adaptable to many designs that utilize a hinge. This is especially useful in prototyping, where you might be testing different hinge designs.
- Visual – The properties of their parent material – polypropylene – allows living hinges to have a smooth and clean look. You’ve probably seen the many colors of bottles down the shampoo aisle at the store, so almost any color is achievable.
- Chemical Resistance– Although polypropylene has less chemical resistance than other plastics, a plastic living hinge is more resistant than metal or ceramic. However, below-freezing temperatures (32F) could cause the hinge to become brittle.
- Durability – Durability is not an issue for this type of design.
- Flexibility – As explained before, the 180-degree rotational flexibility of the hinge is one of the main reasons it is successfully deployed.
- Friction Reducing – When the pivot or hinge line involves two or more pieces there is more friction between the two parts. But with a living hinge, the friction is all but eliminated.
While this list characterizes living hinges in a general sense, there are different designs that each offer a certain advantage. Let’s talk about those different designs in this next section.
Types of living hinges
Straight/ Flat living hinge – A straight hinge is a single or series of hinges that fall along a single axis. There are two types of flat hinges:
-
- Long continuous– These are common with plastic containers- like pencil boxes and clamshell containers. In this case, the hinge connects two long plastic pieces using a single long hinge line.
- Short continuous- The short continuous hinge is common to shampoo bottles. This hinge is shorter and uses what’s called a plastic stop- a piece of plastic that stops the hinge’s rotation at 180 degrees.
Butterfly living hinge – Snip, snap! The butterfly hinge design allows for snappy lid opening and closing. However, because this design has a spring-like function there is a limited range of motion. For example, the lid can only flip to the 90 degrees or 180-degree position depending on the design.
Double living hinge- Now this is unique, a double living hinge! These designs create a gap between the two plastic bodies using two straight hinges separated by a narrow open section. Not to mention this also allows the hinge to rotate a full 360-degrees. A good example of this is an old CD case.
Bi-stable living hinge – A bi-stable living hinge uses three separate hinge sections to perform strong open and closing action. This is very similar to the short continuous flat hinge, except with more hinge. In other words, the bi-stable hinge is stable (or a firm) in both open and closed positions.
Now that you know there are different options for designs, your next question is probably- How are living hinges made? In the next section, we’ll go deeper into the manufacturing techniques used to make a living hinge. Keep in mind, we’ll be focusing on plastic manufacturing.
Manufacturing Techniques To Create Living Hinges
Subtractive manufacturing- CNC Machining
In the prototyping stage, there is no better way to test a design than CNC machining. With a CNC you can machine the plastic down to a couple of thousandths (of an inch) on the hinge. However, polypropylene is notorious for being stubborn and might produce some rough edges. For this reason, you would need to switch to the next manufacturing method when you’re ready for production.
Injection Molding
Injection molding is our bread and butter at PPT, which is why we know how to make living hinges this way. For one, this method is easily the most cost-effective and will produce parts at the highest rate. Second, injection molding produces the most consistency in terms of quality and variation. Therefore, once you nail down your design for manufacturability you can produce consistent parts at a fast clip.
Additive Manufacturing – 3D Printing
3D printing is another popular prototyping method that designers use. In fact, 3D printing allows you to see how a design functions before ever going into production. With this in mind, you can test and adjust your design without sinking thousands of dollars in tooling. The downside to 3D printing is its limited production capability. This is where injection molding comes into play for the long run.
Types of Injection Molding Materials Used For Living Hinges
- Polypropylene (best): Polypropylene (PPE) is a soft, flexible plastic that is best suited for this type of application. This material’s properties allow for that true rotational mobility of 180 degrees. And the material is flexible enough that it won’t snap, crack, or rip at the hinge line. Ultimately, this is the material you’ll want to stick with or change to if you want to design a living hinge.
- Polyethylene: Polyethylene is also a good material to work with. Here, you have one main option: High-density (HDPE) material. The high-density material is thick but easier to machine on a CNC. Furthermore, the hinge line can be made thinner to allow for increased rotational mobility.
Conclusion
In summary, a living hinge is a quality design that can improve the usability and flexibility of your product. And you will benefit from lower manufacturing costs and deal with fewer assembly parts. If you’re curious about how a living hinge design works, or you have a design of your own you would like us to manufacture, give us a call! We’ll help you get up and running in the presses in no time.