The Different Types of Plastic Manufacturing
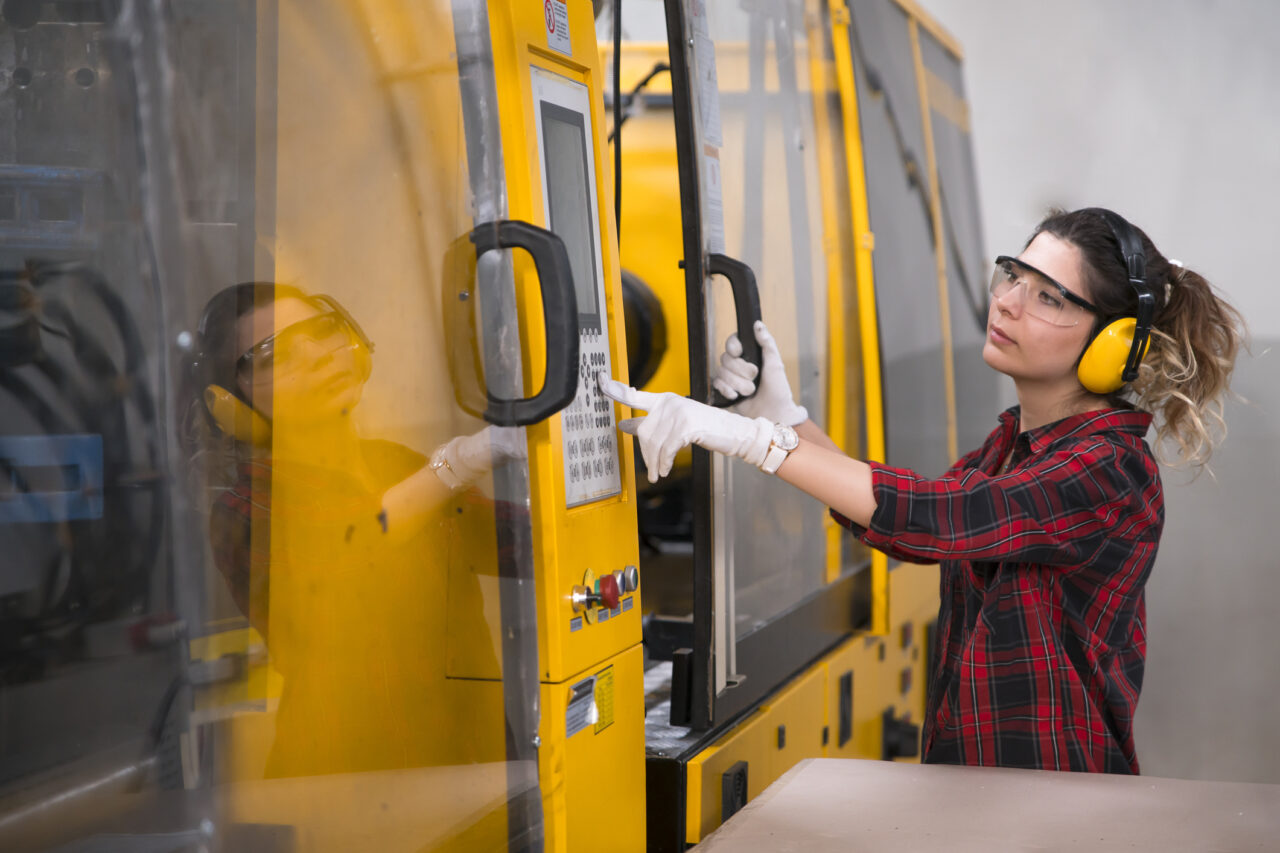
Plastic manufacturing is a popular subject that appears across every industry. From food processing to automotive components, plastic is a staple of the products we use. It’s in our packaging, our transportation, our clothes…it’s everywhere! To meet the high demand for plastic, manufacturers leverage different types of processing capabilities. This includes blow molding, compression, extrusion, rotational, 3D printing, and injection molding. Each one of these methods is capable of producing a specific plastic application. For example, blow molding is best for making plastic bottles, and extrusion is best for tubes. Our service, injection molding, is perfect for mass-producing plastic components.
We’ll discuss these different plastic manufacturing methods in depth throughout this segment. Follow along, or skip to one of the methods of your choice.
What is Injection Molding?
Plastic injection molding is a popular method of making a variety of plastic parts. This process involves melting thermoplastic material through an injection molding machine. First, plastic resin enters the machine via the hopper and enters the barrel. The barrel contains a reciprocating screw, which mixes and melts the plastic. Then, the press injects the molten plastic into a single or multi-cavity mold. The mold clamps shut during injection and open at the end of the cycle. Finally, the cooled part falls from the press and is handled by a machine or an operator.
This is an oversimplified explanation of course, but the capabilities of molding are easy to illustrate. For example, this cycle happens (in most cases) under a minute and sometimes even under 20 seconds. Pair that speed with a multi-cavity mold and you can make thousands of parts a day. Ultimately, this means you can take advantage and scale production quickly.
To wrap up this section (because I could go on) injection molding is fast, scalable, but also repeatable and versatile. The results of injection molding are consistent from run to run, which means you can expect a certain level of quality. And it is versatile because you can make complex 3D shapes. Of course, you have to optimize your design for manufacturability and assembly for it to be moldable. But, if that is taken care of then the possibilities are limitless.
Ultimately, injection molding is best for high-volume production. Whether that application is a medical device, automotive component, or bottle caps; you can produce lightweight, strong plastic parts.
What is Rotational Molding?
Rotomolding is similar in the way that it utilizes a mold to force the plastic to take the desired shape. Except in rotational molding, the polymer is a fine powder that fills the mold. The mold is placed on a rotating arm that operates by moving on a 3-dimensional axis, which helps fill the mold. The mold, while in rotation, enters into an oven that produces heat between 400 and 500 degrees Fahrenheit. The oven encloses the mold for the necessary duration, then moves to a cooling phase. The mold cools under specific conditions dictated by the material and size of the mold.
Rotational molding is a low-pressure manufacturing process. This means that the tooling requirements aren’t as much as other methods, which reduces the cost. For instance, a thin-walled aluminum mold is much less expensive than heat-treated stainless steel used in injection molding. Additionally, there is an opportunity to ‘foam’ rotomolded parts. This means that you can add insulation, floatation, and other capabilities to your product.
Rotational molding is considered a versatile process when it comes to plastic manufacturing. But Rotomolded parts are typically bigger, less precise units that are machined for functionality. So if you want a large plastic unit, like a play structure or a large drum container, rotational molding may be right for you.
What is Blow Molding?
As explained in the introduction, blow molding is great for making plastic bottles. But how does it work? Well, it’s actually like glass blowing but with plastic. You start with a small plastic parison- a rounded mass formed by heating and rolling- and blow gas (air) through it to inflate. Essentially, the small plastic mass inflates according to the shape and size of the mold. Once it cools, the inflated part ejects from the mold.
Blow molding is great for manufacturing one-piece, hollow plastic objects. Like soda bottles! It is also useful for thin-walled applications like plastic storage containers. Like injection molding, blow molding produces high volumes because of its quick cycles. Additionally, there are many thermoplastic materials that are compatible with this process. This creates plenty of opportunities to create specialized products.
What is Compression Molding?
Compression molding is another popular molding method used by automotive part makers. The process is like injection molding, except the mold closes around the plastic during compression. For illustration, the plastic ‘charge is set on the bottom half of the mold. Then, when the press starts the top half smushes the charge into the cavity. The plastic fills the cavity and seeps out into overflow grooves. This is like the runner and gate in injection molding.
Another key difference is that compression molding uses thermoset polymers. This means that after molding, the resulting component must ‘cure’ in a kiln-like oven. Through curing, the component settles into and holds its finished shape.
There are 4 main steps to compression molding:
- A two-part metallic tool matching the exact dimensions of the object is produced, installed, and heated to the requirements of the plastic.
- The plastic composite is pre-formed to the shape of the tool.
- Under pressure, the pre-formed object is inserted in the hot mold and compressed. This pressure ranges anywhere between 800 psi and 2000 psi depending on the thickness of the part.
- The part is removed from the tool and any flash on the edge is trimmed off.
The main benefit of compression molding is the ability to use advanced composite materials. These materials include thermosetting resins, glass-reinforced plastics, fiberglass, and other strong materials. With these materials, you can create a wide range of parts for a variety of applications. Also, with compression molding, you can create simple and somewhat complex geometric shapes. To summarize, compression molding is versatile enough for many low and medium-volume production projects.
What is Extrusion Molding?
The initial process of extrusion molding resembles that of injection molding. The extrusion press uses a screw to melt and push plastic resin through the die. A die, unlike a mold, is a hollow form that shapes the plastic as the screw pushes it through. In other words, the die dictates the specific shape and thickness of the manufactured part. The extruded part is then conveyed into a cooling chamber- a water bath or spray booth. At the end of the cycle, a saw or blade cuts the long extruded material in sections of the desired length.
One key feature of extrusion molding is its continuous process. For example, the extrusion press continuously feeds plastic through the die. This creates a long beam or tube of molded plastic that stays intact until it is cut or wound into a spool. If you haven’t picked up on it yet, extrusion molding is great for long, hollow applications. For example, tubes, straws, pipes, and wires are also extruded applications. Also, channel sections are a popular extruded product as well.
What is Additive Manufacturing (3D Printing)
Additive manufacturing is better known as 3D printing. And it is all the rage in the 21st century. 3D printing uses CAD software and 3D object scanners to program hardware (such as a printer) to make an object. In other words, the digital software recreates an object digitally; which tells the hardware how to physically make it in layers. The 3D printer then produces super-fine layers of material in precise geometric patterns. Layer by layer, the printer deposits material until the final product takes form. This can take minutes, hours, or days depending on the object. But, additive manufacturing is still considered an easier way to develop and test prototype products.
While the technology is advancing, additive manufacturing is still behind in volume capabilities. But, as hinted above, you can skip the wait and test prototypes quicker than other molding processes. For example, with injection molding, you would have to spend thousands of dollars to produce a prototype tool. Not only is that expensive, but the lead times on a tool can set your schedule back. Plus, if for any reason the product is redesigned then that is another costly headache. With 3D printing, you can develop and test prototypes in weeks, not months.
Wrap Up
Now you know the basics of plastic manufacturing! There are a lot more details once you go further into one of these processes. Don’t be discouraged though! There are experts in each of these fields that can help you and understand your challenges. If you’re looking for an injection molder then give us a call!